会社を知る
クロストーク
テーマ新製品開発について
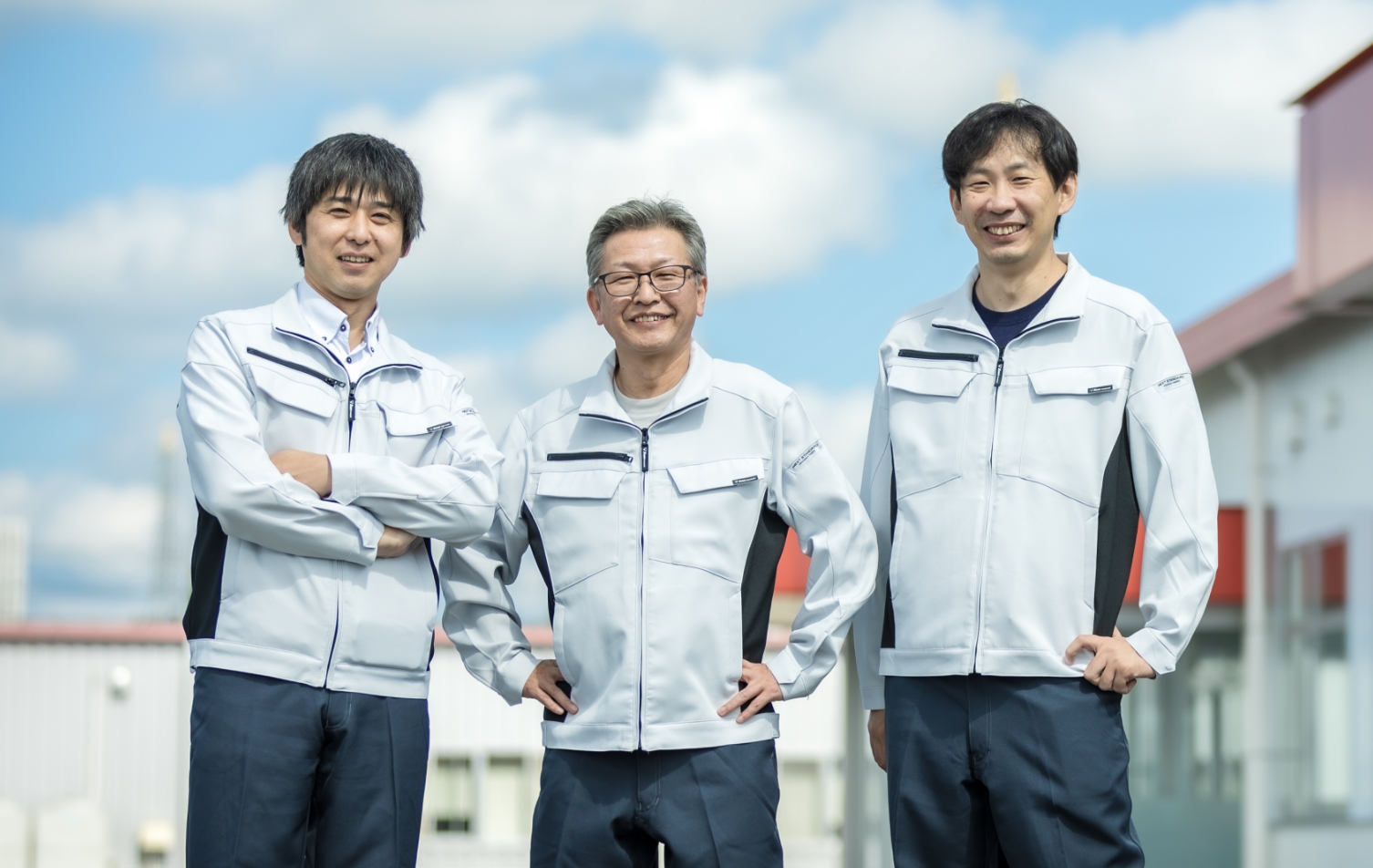
チェックバルブの新製品開発プロジェクトが発足したのは2017年のこと。当時から、製品化に向けて奔走してきた3名の主要メンバーに、立ち上げのきっかけや、量産に至るまでに苦労したこと、今後の展望などをお聞きしました。
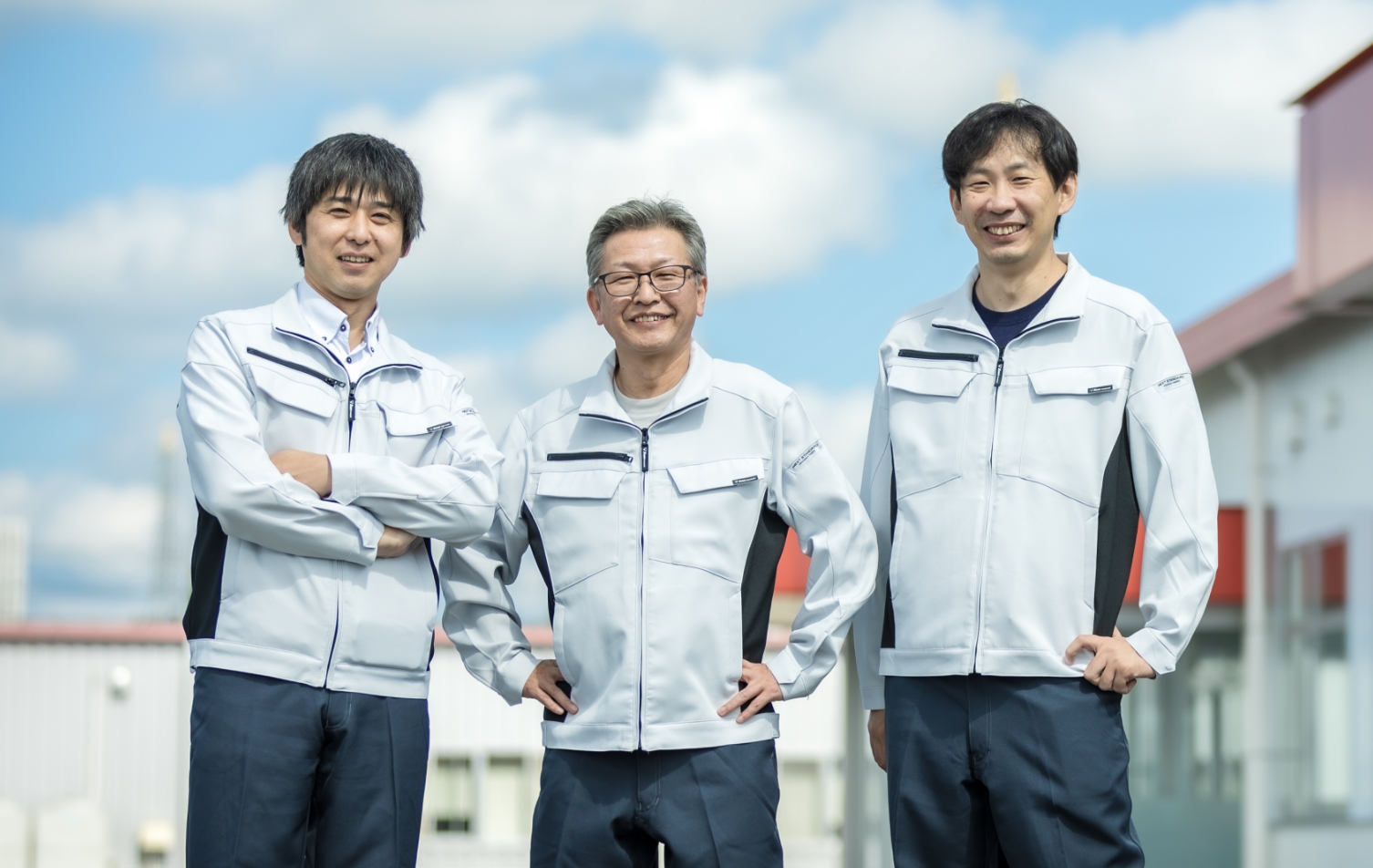
メンバー
-
M.S生産本部 第二福島工場
-
E.N生産本部 白河第二工場 技術グループ
-
F.M事業推進部 生産技術グループ 係長
ゴム製品を扱う会社が複合製品の開発をめざす
どのようなきっかけでプロジェクトがスタートしましたか?
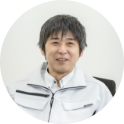
M.S
このプロジェクトは、2017年に発足しました。医療製品に関する勉強会に参加していたとき、「チェックバルブは海外製品が多く、輸入するにも為替や物流の影響を受けてしまう。どうにか国内で生産できないか」と勉強会を主催していたコンサルタントの方からご相談を受けました。
懐かしいですね。それまで、チェックバルブを知らず、透析回路や輸液回路に使用されていて、流体の逆流を防止する部品だと教わりました。製造にあたり、原料には樹脂を使ってほしいと依頼があった時は驚きました。ゴム製品を扱う会社で、樹脂との複合製品をつくる……。なかなかハードルが高いなと思いましたが、新製品の開発は朝日ラバーにとっても大きな案件でしたので、このチャンスを活かしたいと思っていました。
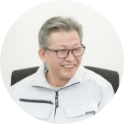
E.N
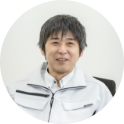
M.S
最初発足した時は、10名ほどのチームでしたよね。第二福島工場と白河第二工場の技術部と営業部が中心になって、進めていきました。私は、プロジェクトの立ち上げから参加していましたが、メーカーとの橋渡し役として、日夜駆け回っていました。
そんなこともありましたね。私は、製品の評価や進捗管理などを担当していました。メーカーの要望を汲んで、設計し形状が定まったら、規格に合っているか、品質は保たれているか、トラブルはなかったかを確認します。ここで、問題がなければ、次の工程へ進みます。
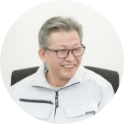
E.N
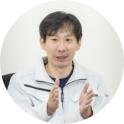
F.M
自分は最終工程である、製品の試作から量産までを担当していました。検査を受けて、使用する機械を選定し、何度も試作を繰り返して、ようやく量産となりました。
実際には、プロジェクトがスタートしてから量産に至るまで、3〜4年かかりました。この間には、コロナの影響もあり、思うように進まない時もありましたが、皆さんの協力のおかげで、なんとか進めてこられました。
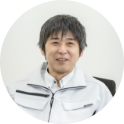
M.S
朝日ラバーの強みを活かして、安心安全の製品をつくりあげる
製品の強みや、製造に関してこだわったところを教えてください。
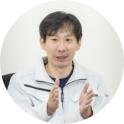
F.M
一番の強みは、製品を全数検査していることですよね。例えば、月100万個出荷するのですが、そのすべてを機能検査装置を使って評価しています。国内生産で、品質も担保されている製品であることが、ユーザーにとって安心感につながります。
「メイドインジャパン」であることは、製品のアピールポイントでもありました。チェックバルブは医療現場で使用されることから、使い回しができず、大量生産が求められていました。そのため、不良を出さずに、安定的に生産するために、機械の導入も進めていきました。
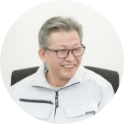
E.N
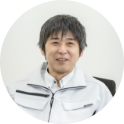
M.S
機能検査装置の選定には、こだわりましたよね。今回、樹脂を使用していたため、満たすべき条件が多く、いくつかの試験をクリアする必要がありました。その甲斐あって、人の手を煩わせずに大量生産できる方法を確立できました。
製品の全数検査を強みとして、自信をもって製造できる体制を構築できたのかなと思っています。現在は、品質管理部門を中心にメンバーも27名と増えたので、より安定した組織で供給を進めていきます。
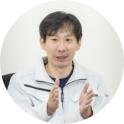
F.M
量産を進めるにあたり、苦労した点はありましたか?
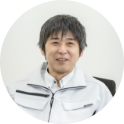
M.S
正直、苦労した点は沢山ありました。これまでゴム製品しか扱ったことがなかったので、どう製品に落とし込んでいけばいいのかわからず……。近隣の樹脂を扱うメーカーさんに何度も通うほか、樹脂製品に関するYouTube動画をみて、知見を深めていました。
今考えると、なかなか難しいことをしていましたよね。やはり一番苦労したことは、お客様によって要望が異なっていたり、使用用途によって仕様が変わったり。製品のカスタマイズと検査を同時に進めていく場面もあったので、製品開発の難しさを感じていました。
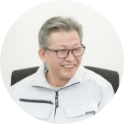
E.N
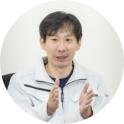
F.M
同感です。新製品を開発する場合、JIS規格への準拠が求められるのですが、これには苦労しました。チェックバルブでいうと、一定時間内に圧力をかけて、どのくらい耐えられるか試したり、液体を気体に置き換えたときどうやって試験・評価するか悩んだり、試行錯誤しながら、規格を検討していきました。
それぞれ苦労したことはあったと思いますが、新製品の開発を通して、成長したこともありましたよね。
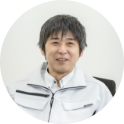
M.S
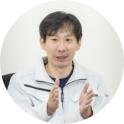
F.M
そうですね。これまで、現場にいた期間が長かったので、開発に携わるようになって、とにかく勉強の毎日でした。金型の設計、装置の導入、JISやISOに関する知識の習得と、学んで経験することによって、新たな視点でものづくりに取り組めるようになったと感じています。
みんなで学びながら切磋琢磨するのも、製品開発の醍醐味ですよね。ゴム単独の製品とはちがって、ゴムと樹脂の複合製品は不良の出方や特性が異なります。チェックバルブ自体は小さな部品ですが、多くの方の技術や想いがここに詰まっていると思うと、これまでの苦労も無駄ではなかったと感じます。
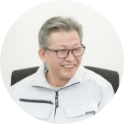
E.N
大きな挑戦を経て、それぞれが成長した7年間
プロジェクトを経て、今後の展望を教えてください。
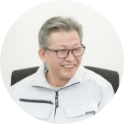
E.N
この7年間で、チェックバルブの量産が進み、異なる形状の製造もはじめました。今後は、部品としてだけでなく、実用品に近い形まで製造できるよう、ノウハウを身につけていきたいと思います。
これまで生産・製造を中心に仕事をしてきて、新製品の開発、しかもゴムと樹脂の複合製品というむずかしい課題に挑戦しました。今後、この経験を活かしていきます。また、これから少子高齢化により働き手が減っていくなか、設備の自動化を進める必要性があるため、省人化による利益率の向上と、チェックバルブの発展に貢献していきます。
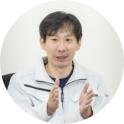
F.M
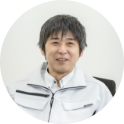
M.S
朝日ラバーの仕事は、図面をもらって製品化を支援するという「請負」が中心で、ゼロから新製品の開発に携わることは少なかったと思います。その点、今回のプロジェクトは、仕事の幅を広げるとともに技術力を高める絶好の機会でした。また、チェックバルブは国内だけでなく、アジアでの現地生産を視野に、世界市場へと拡大する可能性を秘めている製品です。私自身、後輩社員たちとともに、これからの成長を見届けたいと思います。